Fehlteile aus der Spritzerei sollen mit einer Durchsatzleistung von 200 – 300 kg/h mit geringstem Personalaufwand zerkleinert werden. Die Fehlteile werden in Behältern gesammelt und sollen vom Bediener in die Anlage entleert werden. Die Behälter werden nicht einzeln sondern mehrere nacheinander aufgegeben.
Das Mahlgut muss staubfrei sein und die Körnergrößen in einem kleinen Verteilungsspektrum liegen. Mögliche metallische Verunreinigungen müssen automatisch sicher entfernt sein. Die Abfüllung des Mahlguts erfolgt in vier unterschiedliche Container.
Auslegung der Anlage:
Die Kunststoffteile besitzen kleine Abmessungen (kleiner 100 mm) und lassen sich aus einem Behälter gut auskippen oder dosieren.
- Die Behälter werden in einen Teilebunker ausgeleert. Die Austragsrinne des Teilebunkers dosiert die Spritzgussteile mittels Vibration auf ein Förderband. Dieses Förderband beschickt den RotoSchneider RS 3004.
- Im Förderband ist ein Metalldetektor integriert. Metall-Alarm schaltet eine pneumatische Klappe am Trichtereingang des RotoSchneiders. Das verunreinigte Material fällt durch die entstehende Öffnung in bereitgestellte Boxen und kann zu einem geeigneten Zeitpunkt von den Bedienern betrachtet werden.
- Der RotoSchneider RS 3004 läuft mit einer Rotordrehzahl von 300 Upm und sorgt so für einen niedrigen Schallpegel und sehr staubarmes Granulat.
- Ein Transportgebläse fördert das Granulat zu einer Entstaubungsanlage. Durch das Windsichtverfahren erhält man 99,9 % staubfreies Granulat.
- Dieses Granulat wird nochmals mittels eines Allmetallseparators überprüft.
- Fördergebläse transportiert das Granulat zu den drei Speichercontainern. Die Container können über pneumatische Weichen einzeln angesteuert werden. Füllstandssensoren in den Containern informieren über den Füllungsgrad.
- Eine kleine SPS steuert die automatische Beschickung des RotoSchneiders nach seiner leistungsmäßigen Auslastung und füllt das entstehende Granulat nacheinander in die bereitgestellten Container ab.
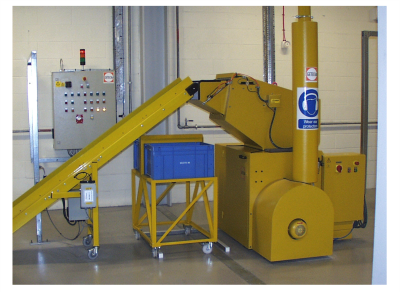
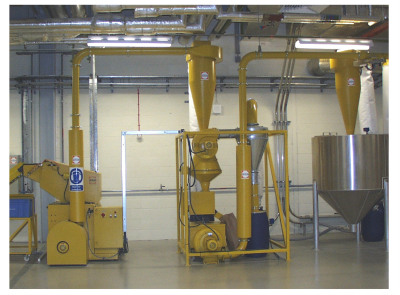